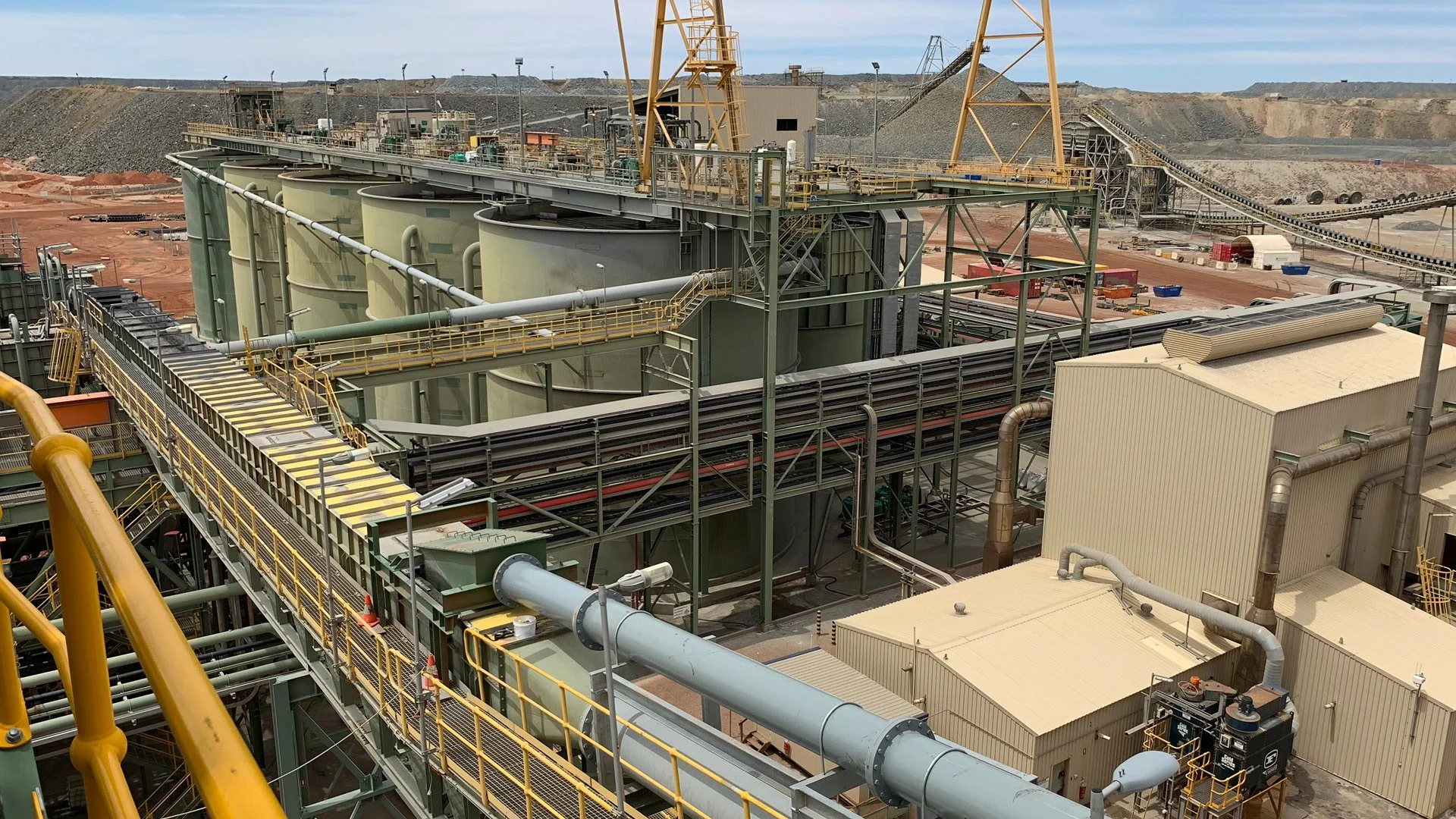

Tropicana Gold Project Design
Project Category: Process Design, Optimisation
Client: AngloGold Ashanti Australia (AGA)
Location: 330km SW Kalgoorlie, WA
Capacity: 8.6 Mtpa
Commodity: Gold
Scope of Work
Process design (comminution option study and final circuit design) and commissioning services via Lycopodium Minerals Pty Ltd for the Tropicana Gold Plant.
Commissioning and ongoing Optimisation support was provided to AGA via the OMC’s remote grinding support (RGS) service.
Optimisation studies throughput the life of the project including surveys and model fitting to allow for de-bottlenecking studies of the existing equipment over the life of the project.
Expansion study using plant survey models to conduct option studies and final mill selection.
Commissioning and ramp-up support for the expansion.
Flowsheet
The comminution circuit comprised a primary gyratory crusher and coarse ore stockpile, closed circuit secondary cone crushing and screening, closed circuit HPGR grinding and wet screening, followed by a closed-circuit ball mill and cyclones. A second parallel ball mill was commissioned in 2018.
Notable Features
Prediction of HPGR recirculating load and appropriate selection of conveyors and screens, ball mill design where HPGR crushed feed is a factor, testing oxide content design limits for a HPGR. Setting up a control system to automate throughput control to grind. Integrating a second ball mill into the existing control philosophy to maximize power utilization post upgrade.
Outcome
The plant was commissioned on schedule and ramp-up to full production was achieved within three months of first gold pour, notably faster than comparable HPGR circuits.
On-going optimisation allowed for continued ramp up to +800tph, or 6.4Mtpa well above the original circuit design of 5.5 Mt/a. This included working with AGA site personal to implement changes to various operating set points and equipment configurations, development of the grinding circuit control philosophy and developing appropriate operating strategies for different feed types and other operating challenges. Power efficiency improvement was also a focus during optimisation studies, with a 15% improvement in power efficiency achieved in the milling circuit while simultaneously increasing throughput.
Selection of the most cost-effective expansion option and ramp-up support following addition of a second mill to increase circuit capacity to 8.5 Mt/a.

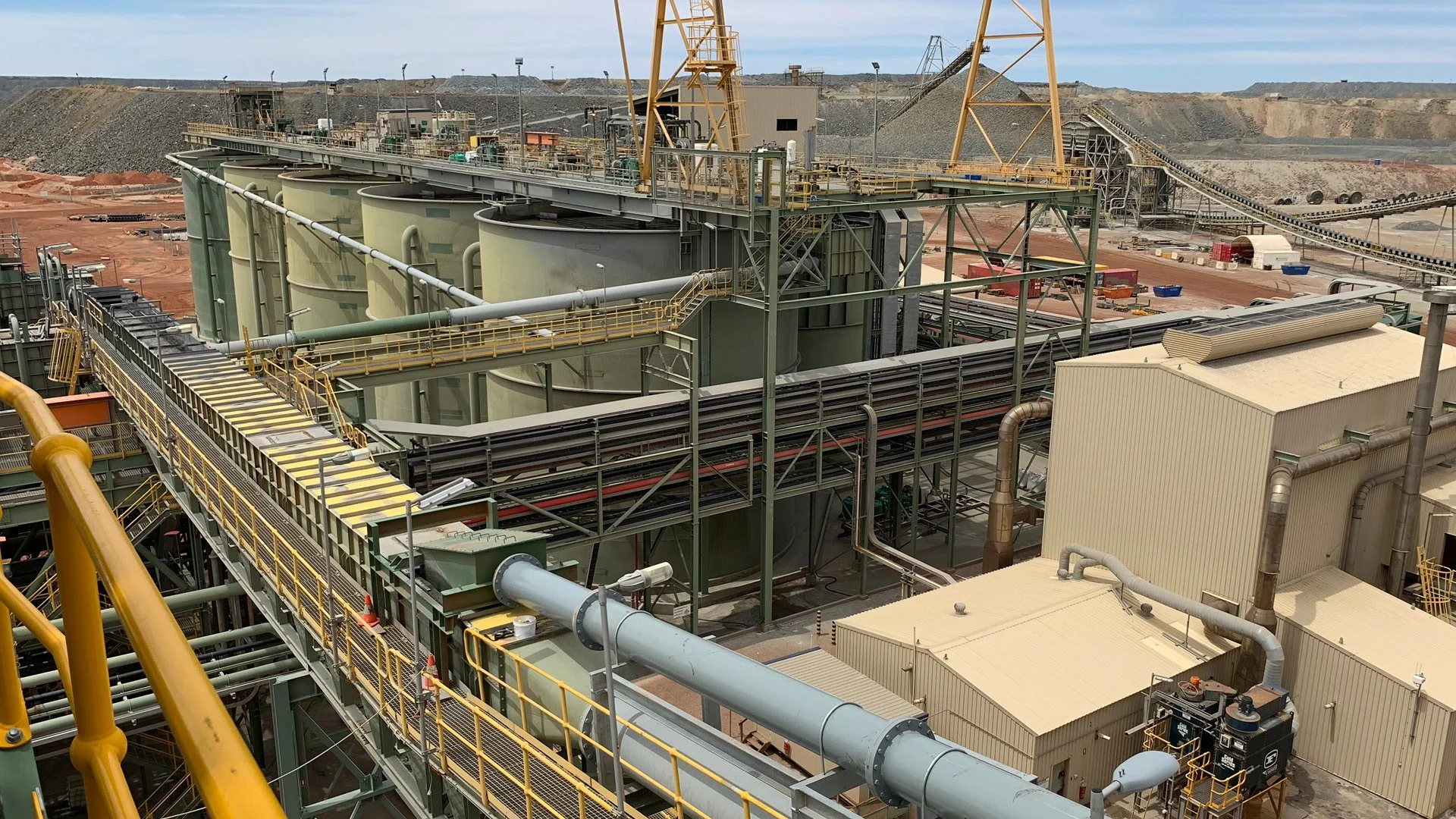
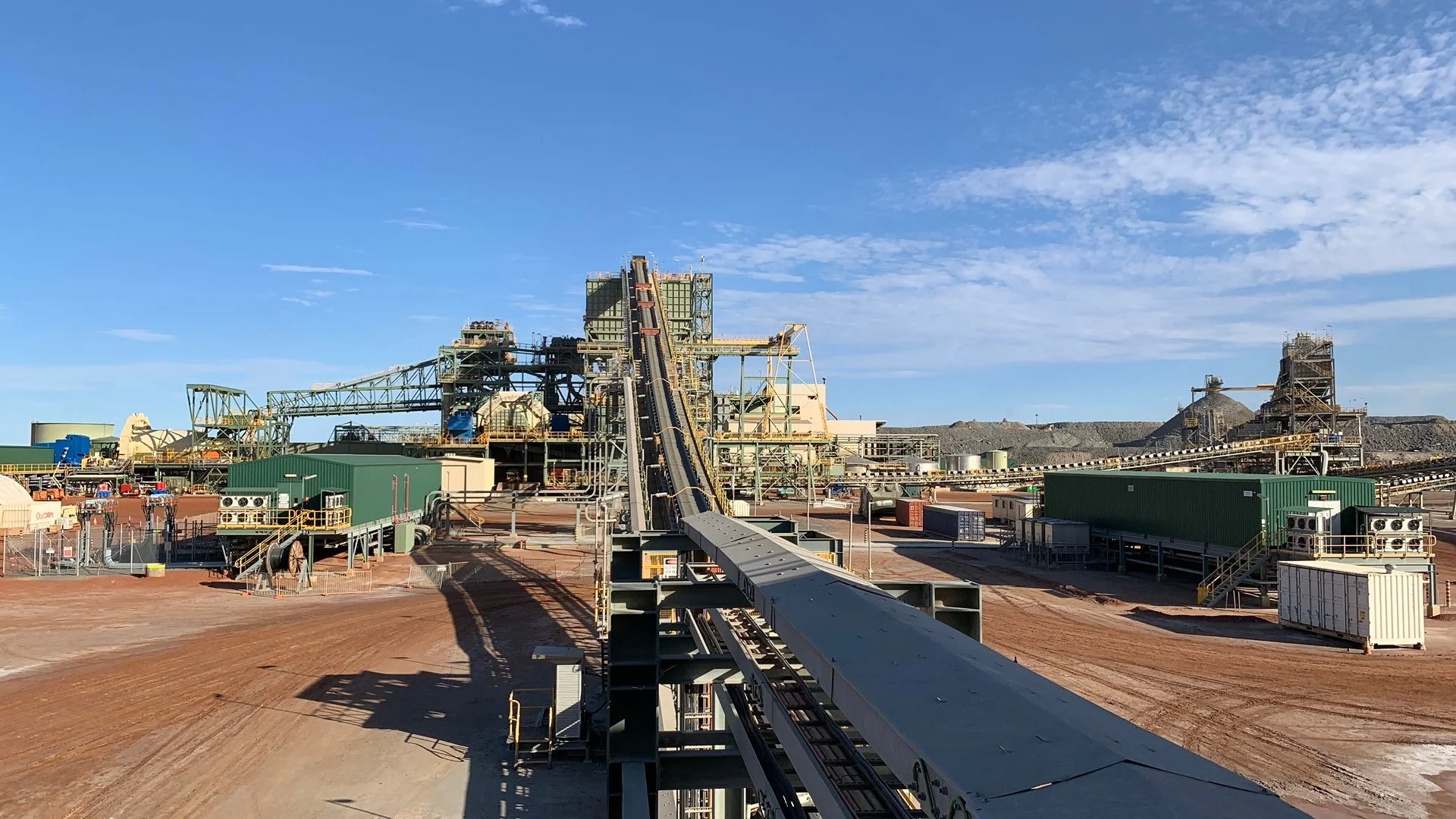
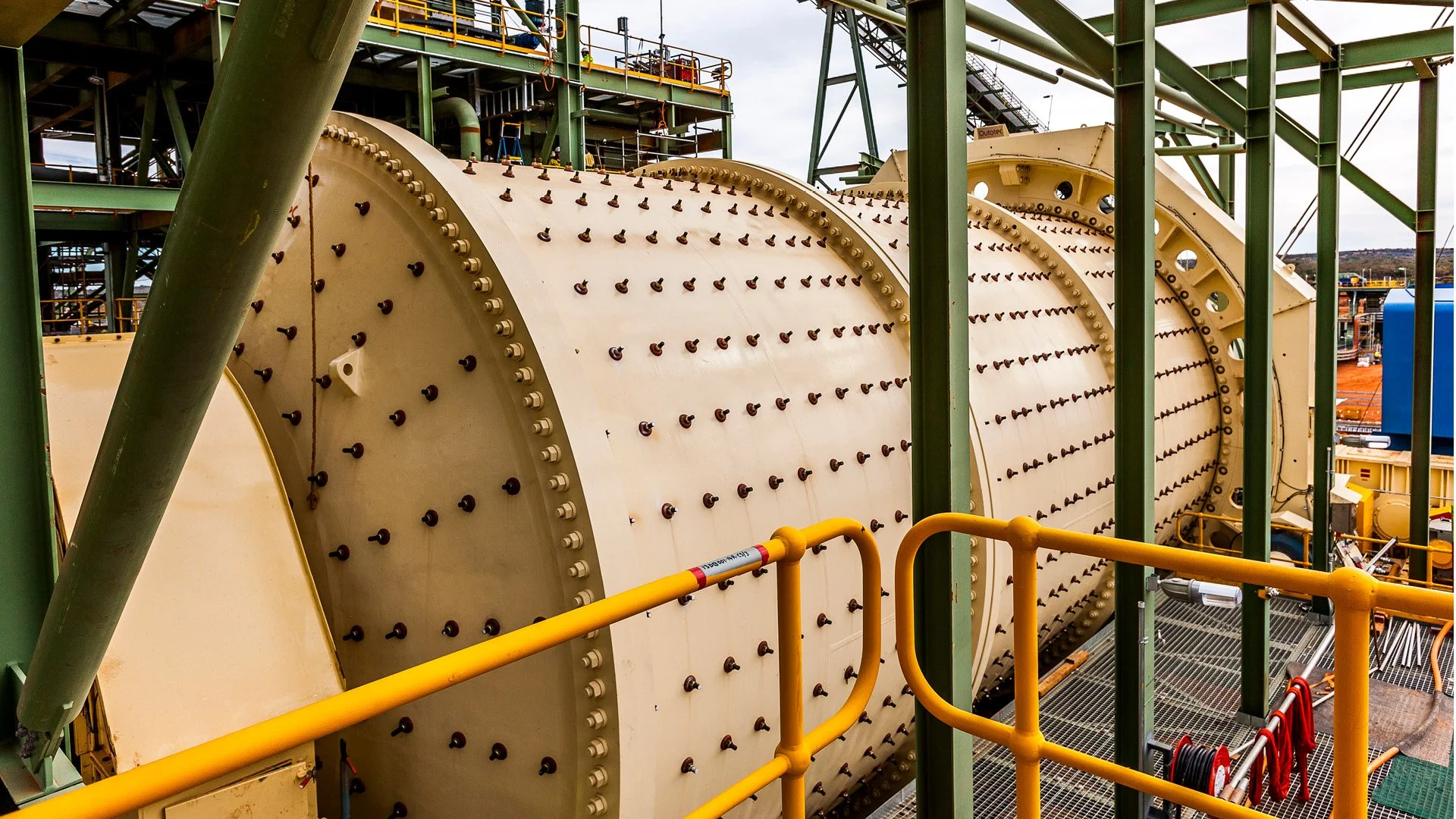