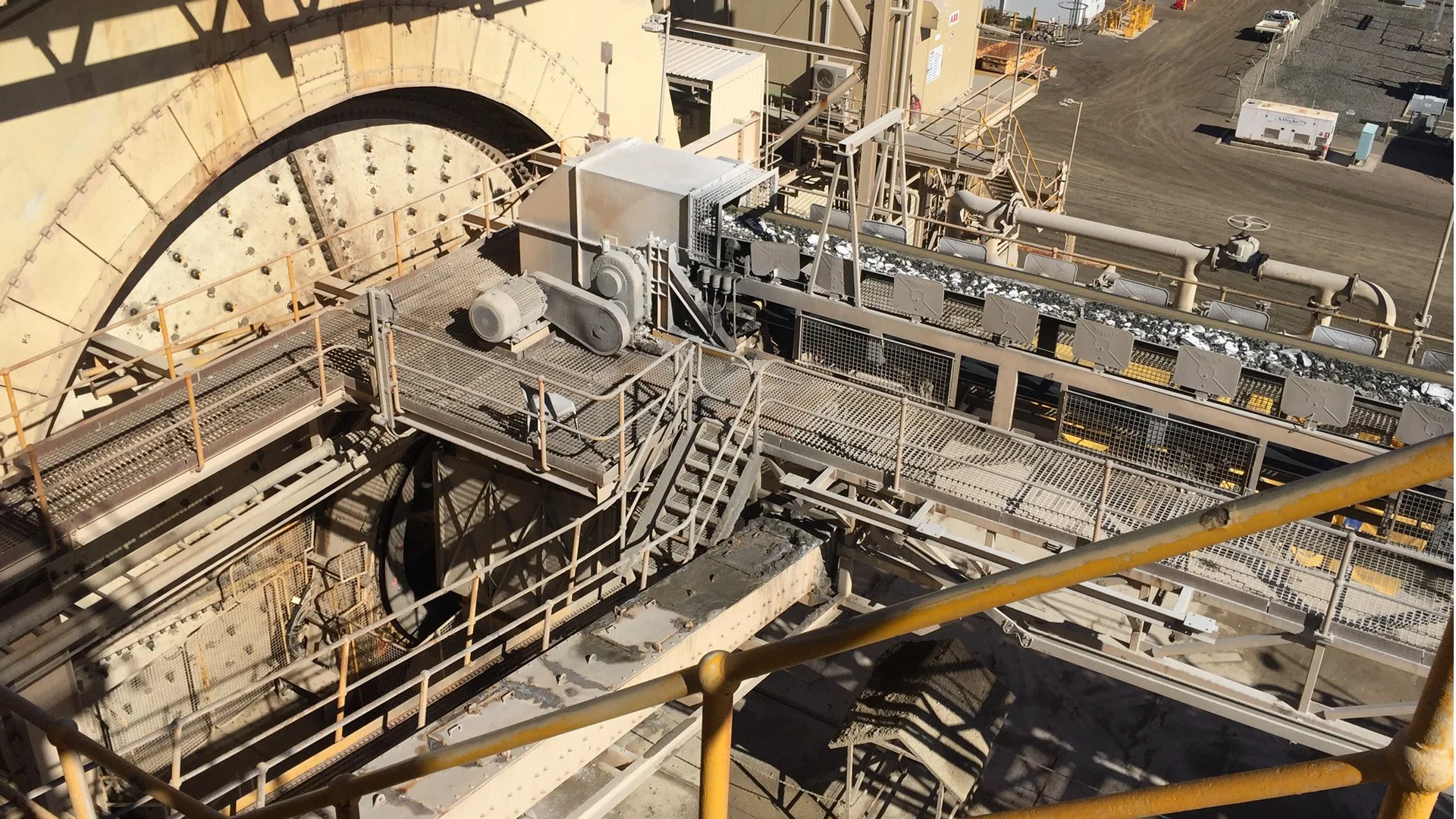
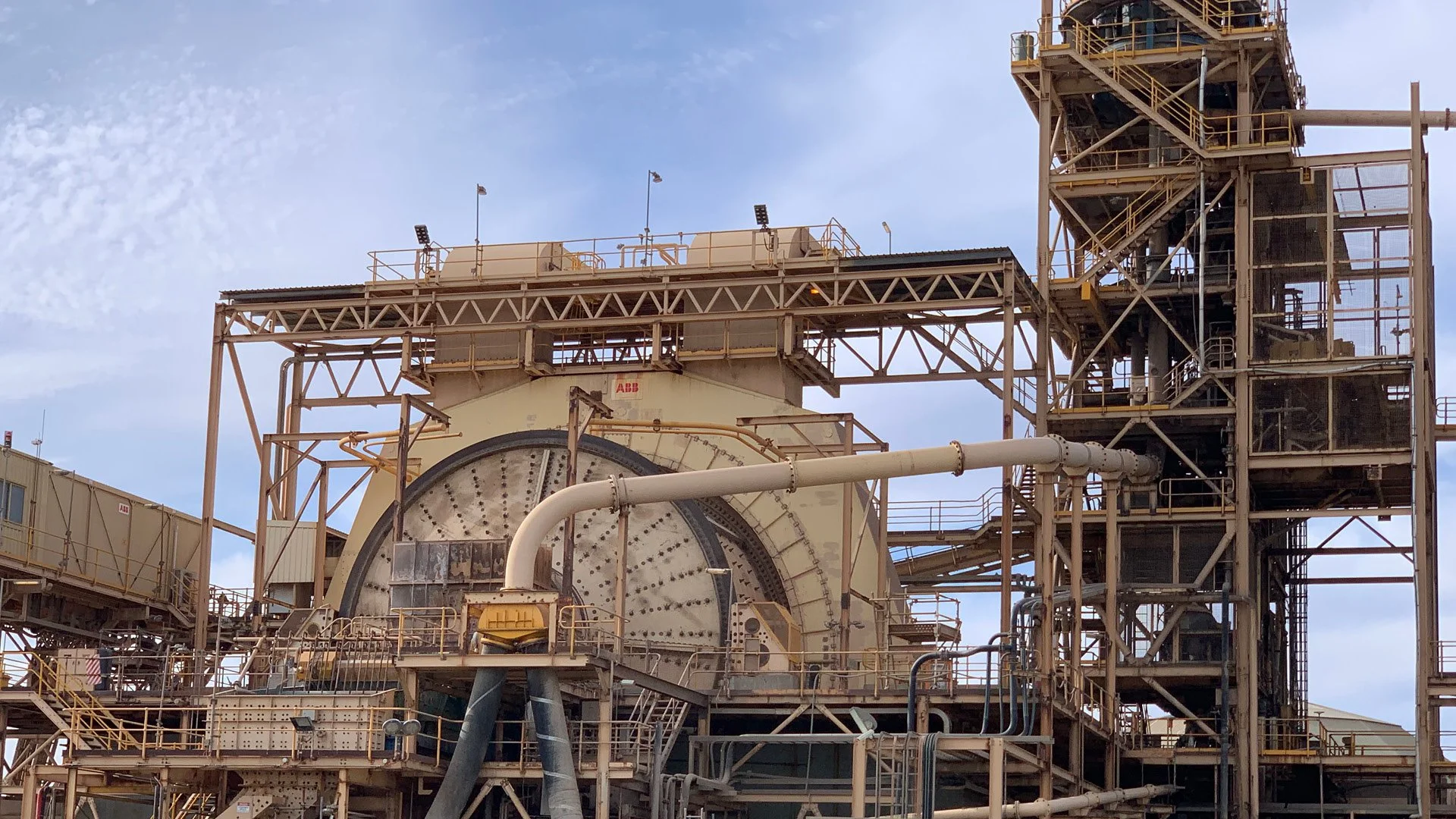
GOLD PROJECT (WA 2)
Project Category: Optimisation
Location: Western Australia
Capacity: 4.5 Mt/a
Commodity: Gold
Scope of Work
Orway’s scope of work was to optimise the project, reviewing circuit performance and undertaking a grinding circuit survey.
Flowsheet
The circuit comprised primary crushing followed by a single stage SAG mill with recycle crusher.
The primary crusher is a 54/77 gyratory crusher, 600 kW. The SAG mill is 10.97 m in diameter (inside shell) and has an effective grinding length (EGL) of 5.49 m. The steel lined mill is fitted with a 13,000 kW gearless motor (with variable speed). The SAG mill discharges over a vibrating screen, 3.66m W x 8.54 m L. Screen oversize is conveyed to the pebble crushing circuit with the underflow reporting to the discharge hopper. The pebble crusher is a Sandvik CH660, which receives feed from the pebble crusher surge bin (50t capacity) and discharges directly onto the SAG mill feed conveyor. The screen undersize material is pumped to the cyclone cluster for classification, with the cyclone overflow reporting to the trash screens.
Notable Features
The SAG mill was running slowly with high ball charge and minimal autogenous media. The grind was coarser than target and the cyclones regularly roped causing issues with the trash screen and CIL.
To improve stability, grinding efficiency and to reduce media costs the following recommendations were made:
The pebble crusher should be bypassed and should only be bought online if maximum SAG mill speed is reached or over grinding is occurring.
The ball charge should slowly be reduced. As the amount of steel media is reduced it must be replaced with autogenous media and increase SAG mill speed to draw power. To aid the build-up of autogenous media a larger closed side set should be trialled on the primary crusher. This is essentially a move back to pre-2017 levels, ball charge circa 8% and a primary crusher closed side set 125 to 150 mm.
The cyclones should be changed to constant pressure for control.
Outcome
Working with the site team, the circuit was transitioned from a ROM ball mill back to a low ball charge SAG mill operating at higher mill speed as recommended providing a number of benefits including:
Allowing the SAG mill to operate at higher speed utilising more of the installed power, +6%.
Providing fine autogenous media for grinding, increasing the milling efficiency by an estimated 13%.
From the production data the 6% additional power draw and 13% improvement in milling efficiency was used to achieve a 6% increase in throughput and a reduction in the grind size from P80 150 μm to 114 μm.
The reduced grind resulted in 1.5% increase in gold recovery, statistically confirmed by site.
The finer grind and more stable circuit reduced issues with roping of the cyclones, reducing the sand fraction reporting to the trash screen and into the CIP circuit, improving carbon management. The trash screens which used to be constantly overloaded with sand only then very rarely overflowed.
The move to more autogenous grinding more than halved the SAG mill ball consumption, saving more than $1M per year.
These benefits combined have resulted in millions of dollars of improved revenue and reduced operating costs.

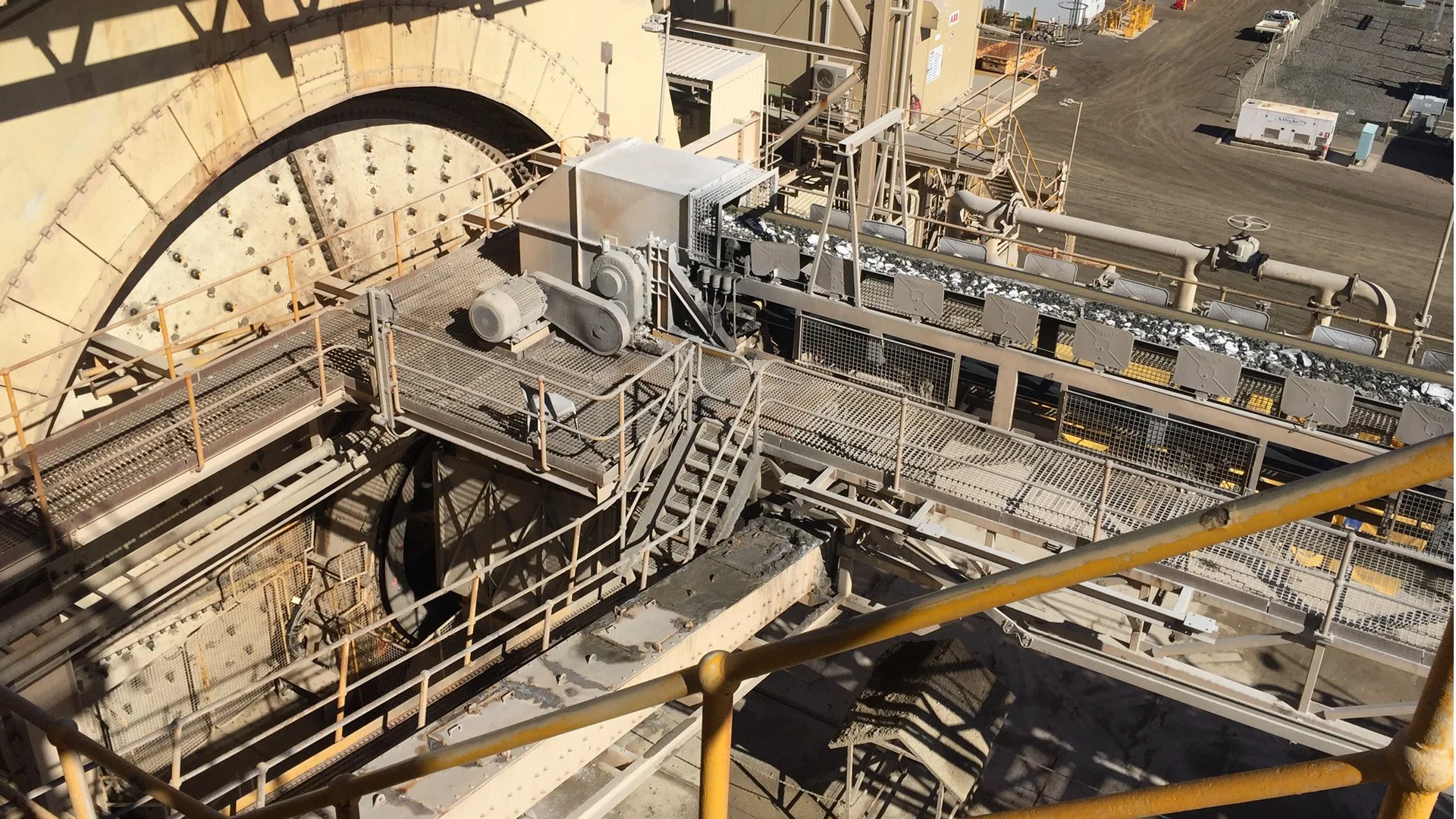

